Diamond Blades have evolved quite a bit over the past 20 years. New manufacturing processes have allowed engineers to get creative with blade design. This has significantly increased the amount of cool features diamond blades can have. One of the most important diamond blade metrics to track is cutting speed. This makes turbo segmented diamond blades one of the most interesting factors to consider with blades.
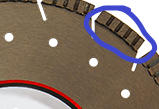
Whenever I am training a new employee I show them 5 or 6 different kinds of blades. I ask them what feature they think makes a blade cut fast, and what do they always answer? Turbo segments? Nope, they assume that cooling holes in the blade core make the blade cut fast. This is only partially true. Most turbo diamond blades incorporate cooling holes because the blades cut faster , heat up quicker and burn out. The cooling holes allow the blade to aerate and stay a little cooler, which prolongs the blades life.
The actual reason a diamond blade is considered turbo is the actual segment on the blade. Once the blade is ridged or rippled, it creates more speed on the saw. The cutting action is increased and the blade cuts much faster than a traditional diamond blade without turbo segments.
Realistically, I would estimate a turbo segmented diamond blade cuts 5%-10% faster than the same blade without turbo segments. This inevitably will cut down on the blades life. In my opinion, speed is always the way to go, I’d much rather be slicing through material fast and spend a little more, than cutting slow and saving a few bucks.
Category: Uncategorized