Ductile iron cutting diamond blades are specialized cutting tools designed for cutting through ductile iron, a material known for its high strength and toughness. These blades are typically made using a combination of diamond particles and a metal matrix, which are then bonded together to create a high-performance cutting tool.
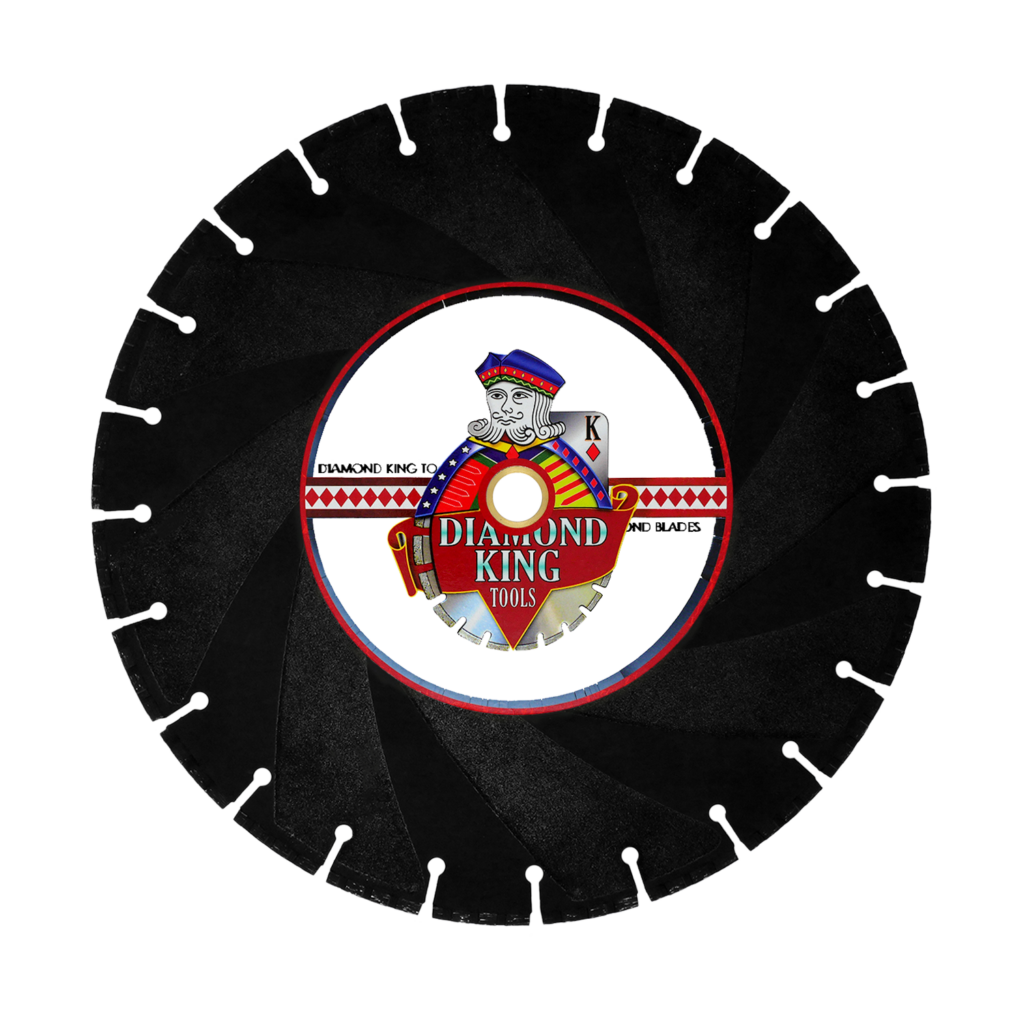
Manufacturing Process:
- Powder Mixing: The first step in the manufacturing process is to mix the diamond particles with a metal powder such as cobalt, nickel, or iron. This mixture is then placed in a mold to create the desired blade shape.
- Sintering: The mold is then placed in a sintering furnace and heated to a high temperature, causing the metal powder to melt and bond with the diamond particles. This process creates a solid metal matrix with embedded diamond particles.
- Segment Forming: The blade is then cut into individual segments using a laser or other cutting tool. The segments are then shaped to the desired size and shape using a grinding wheel.
- Segment Bonding: The segments are then bonded to the blade core using a high-strength adhesive, such as epoxy or resin. The blade is then assembled and balanced to ensure smooth and efficient cutting.
- Quality Control: Finally, the blade undergoes rigorous quality control testing to ensure it meets industry standards for performance and durability. This may include testing the blade’s hardness, diamond particle distribution, and cutting speed.
Overall, the manufacturing process for ductile iron cutting diamond blades is a complex and precise process that requires specialized equipment and expertise. The result is a high-performance cutting tool that can handle the toughest materials with ease.